Seal the Deal: Why Heat Seal Testers Are Essential for Packaging Quality Control
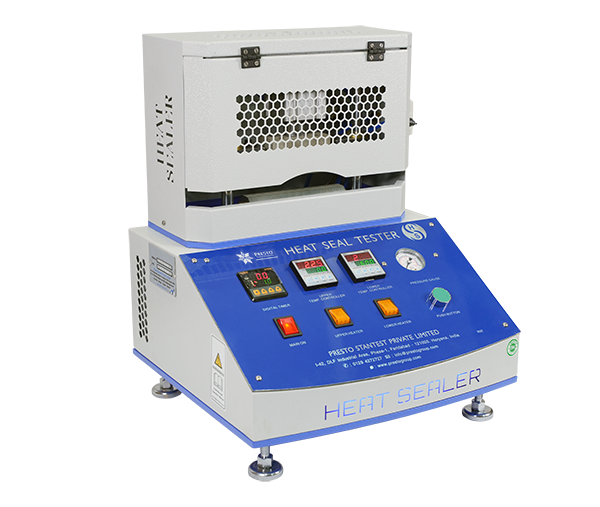
In the competitive world of packaging, product safety and durability are paramount. One of the most critical elements in ensuring packaging integrity is the sealing process. A faulty seal can compromise the product’s quality, shelf life, and consumer satisfaction. This is where the heat seal tester comes into play—a vital quality control instrument used across various industries to test and validate heat-sealed joints in flexible packaging materials.
What Is a Heat Seal Tester?
A heat seal tester is a specialized laboratory instrument designed to evaluate the sealing strength of flexible packaging materials such as plastic films, foils, laminates, and multi-layer substrates. By simulating real-world sealing conditions, it ensures that the seals are strong enough to withstand pressure, heat, and handling during transport and storage.
The primary function of the heat seal tester is to replicate the sealing process and test how well the material responds to controlled temperature, pressure, and dwell time. This helps in determining the optimal settings for packaging lines and verifying seal strength consistency across production batches.
The Role of a Heat Sealer in Packaging
A heat sealer is the machine responsible for bonding packaging materials using heat and pressure. Whether in the food, pharmaceutical, or consumer goods industry, heat sealers are indispensable. However, without proper testing, even a top-tier heat sealer machine may produce unreliable seals due to material variability or improper settings.
That's why combining a heat sealer machine with a heat seal tester for packaging creates a robust quality assurance system. The tester provides actionable insights into sealing performance, allowing manufacturers to fine-tune the sealer’s parameters for maximum efficiency and safety.
Why Is Heat Seal Testing Important?
-
Ensures Package Integrity: The seal is often the first line of defense against contamination, leakage, and spoilage. Heat seal testing ensures seals hold up under stress and prevent product failure.
-
Compliance with Standards: Industries such as pharmaceuticals and food processing are governed by strict packaging standards. Using a heat seal tester helps companies comply with regulatory guidelines like ASTM F2029 or ISO 11607.
-
Reduces Product Waste: Poor seals can lead to product recalls and waste. Early identification of sealing issues via a heat seal tester can prevent costly errors in production.
-
Enhances Consumer Trust: Delivering a well-sealed product that maintains freshness and quality builds brand reputation and customer loyalty.
Applications Across Industries
The heat seal tester for packaging finds applications in:
-
Food packaging: To ensure vacuum-sealed or modified atmosphere packaging (MAP) is secure.
-
Pharmaceuticals: To prevent contamination and ensure child-resistant closures.
-
Cosmetics: To avoid leakage during storage or transit.
-
Electronics and industrial components: To maintain protection against moisture and dust.
Choosing the Right Heat Seal Tester
When selecting a heat seal tester, consider the following factors:
-
Temperature Range: Ensure the tester can reach the required heat levels for your material type.
-
Pressure Control: Accurate pressure application is essential for consistent results.
-
Dwell Time Settings: A customizable dwell time allows precise testing aligned with real production conditions.
-
Compatibility: The tester should be compatible with your existing heat sealer or heat sealer machine setup.
Conclusion
In today’s fast-paced and quality-driven market, the heat seal tester is a crucial tool for any manufacturer committed to delivering durable, safe, and high-quality packaging. Whether paired with a heat sealer or used independently in R&D labs, this device plays a central role in quality assurance processes. For businesses aiming to improve packaging performance, investing in a reliable heat seal tester for packaging is a smart and strategic decision.