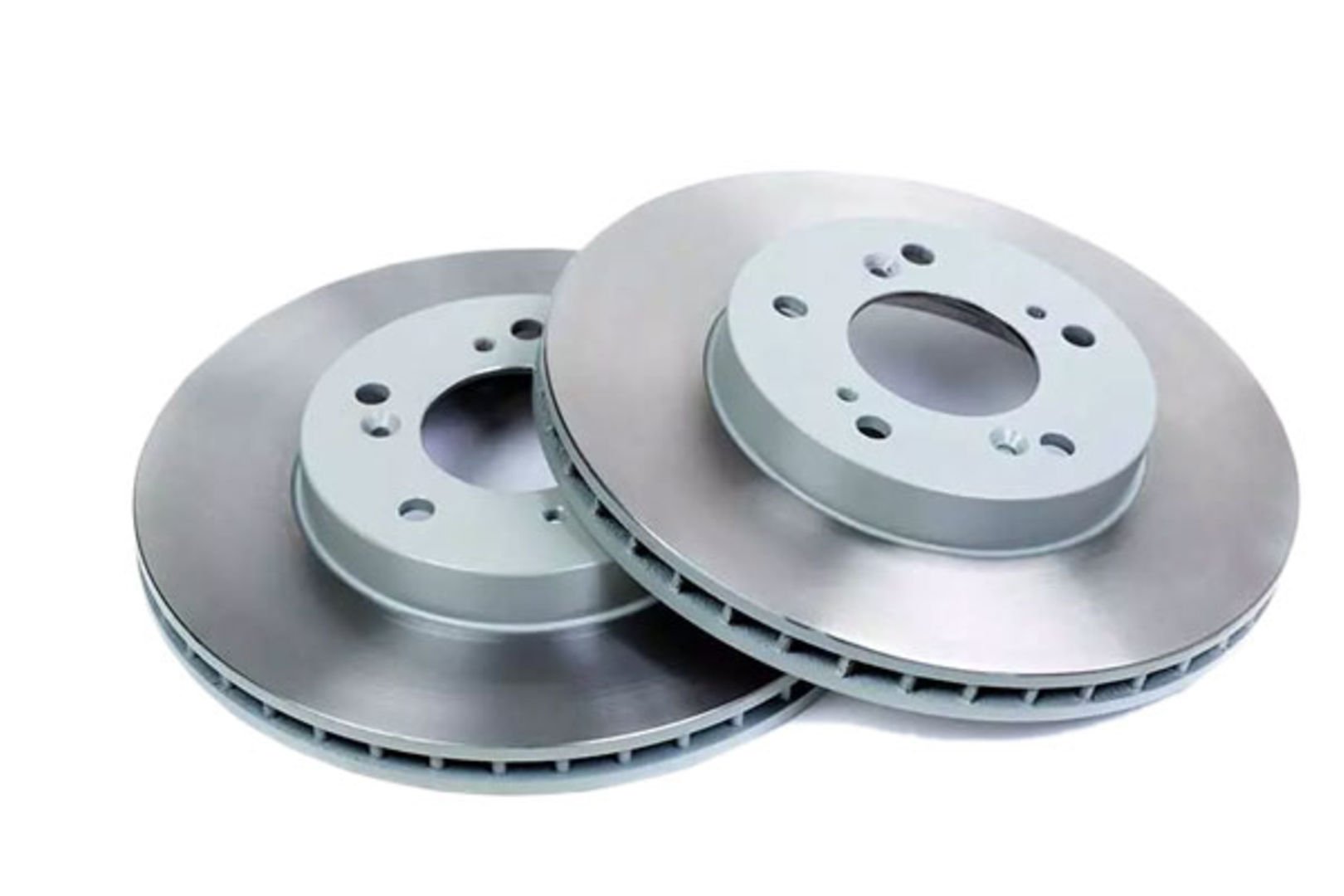
Automotive Brake Rotor Manufacturing Plant 2025: Project Report, Manufacturing Process, and Setup Cost
- Feb 05, 2025
- | 14
Automotive brake rotors, also known as brake discs, are important components of a vehicle's braking system, ensuring safety and performance on the road. Typically made from cast iron, carbon composites, or ceramic materials, brake rotors come in various designs, such as solid, vented, slotted, or drilled, each catering to specific driving conditions and vehicle types. The primary role of brake rotors extends beyond deceleration, as they play a critical part in dissipating the heat generated during braking, thereby maintaining the system's efficiency and longevity. Their applications span across passenger cars, commercial vehicles, and high-performance sports cars, underlining their universal importance in the automotive industry.
The global demand for automotive brake rotors is driven by several factors, beginning with the consistent growth in vehicle production and sales worldwide. The increasing emphasis on road safety regulations and stringent braking performance standards has made high-quality brake rotors a necessity. Also, the growing popularity of electric as well as hybrid vehicles has further accentuated the demand for lightweight and efficient rotors, as these vehicles require optimized braking systems to complement their energy recovery processes. The surge in the adoption of advanced driver-assistance systems (ADAS) has also significantly boosted the market, as these systems rely on precise and reliable braking mechanisms. Furthermore, the expansion of the automotive aftermarket and the rising consumer awareness regarding timely vehicle maintenance are encouraging the replacement and upgrade of brake rotors, driving steady market growth.
IMARC Group’s report titled “Automotive Brake Rotor Manufacturing Plant Project Report 2025: Industry Trends, Plant Setup, Machinery, Raw Materials, Investment Opportunities, Cost and Revenue” offers a comprehensive guide for setting up an automotive brake rotor manufacturing plant.
Request for a Sample Report: https://www.imarcgroup.com/automotive-brake-rotor-manufacturing-plant-project-report/requestsample
The report includes the following information:
Market Analysis:
The automotive brake rotor market is witnessing transformative trends, starting with the increased adoption of lightweight materials such as carbon composites and ceramics to improve fuel efficiency and reduce carbon emissions. Additionally, the integration of smart braking technologies, such as electronic brake rotors with embedded sensors for real-time performance monitoring, is emerging as a significant innovation. Lastly, the growing penetration of electric vehicles and the proliferation of autonomous driving technologies are expected to fuel the demand for next-generation brake rotors, designed for seamless integration with cutting-edge vehicle systems, paving the way for a futuristic, safer, and more efficient driving experience.
- Market Trends
- Market Breakup by Segment
- Market Breakup by Region
- Price Analysis
- Market Forecast
Project Overview
This section offers detailed information related to the process flow and several unit operations involved in a automotive brake rotor manufacturing plant project. Moreover, information related to raw material requirements and mass balance has further been provided in the report with a list of necessary technical tests as well as quality assurance criteria.
- Product Overview
- Unit Operations Involved
- Mass Balance and Raw Material Requirements
- Quality Assurance Criteria
- Technical Tests
Key Requirements and Costs
This section provides an analysis encompassing insights, including land location, selection criteria, location significance, environmental impact, and expenditure for automotive brake rotor manufacturing plant setup. Besides this, the report further offers information related to plant layout and factors influencing the same. Additionally, other expenditures and requirements related to packaging, utilities, machinery, transportation, raw materials, and human resources have also been included in the report.
- Land, Location and Site Development
- Plant Layout
- Machinery Requirements and Costs
- Raw Material Requirements and Costs
- Packaging Requirements and Costs
- Transportation Requirements and Costs
- Utility Requirements and Costs
- Human Resource Requirements and Costs
Browse the Full Report with the Table of Contents: https://www.imarcgroup.com/automotive-brake-rotor-manufacturing-plant-project-report
Project Economics:
This section covers a comprehensive analysis of the project economics for setting up a automotive brake rotor manufacturing plant. This comprises the analysis and detailed understanding of capital expenditure (CapEx), operating expenditure (OpEx), taxation, depreciation, profitability analysis, payback period, NPV, income projections, liquidity analysis, uncertainty analysis, and sensitivity analysis.
- Capital Investments
- Operating Costs
- Expenditure Projections
- Revenue Projections
- Taxation and Depreciation
- Profit Projections
- Financial Analysis
Customization Available:
Production Capacity:
Draft the machinery selection and plant layout to align with the expected scale of production, which can range from small-scale operations to large industrial setups.
Automation Levels:
Modify the level of automation based on labor availability, budget constraints, and technical expertise from semi-automated processes to fully automated systems.
Location Adaptation:
Customize the plant's location to strategically align with local market demand, ensure efficient access to raw materials, utilize available labor resources, and adhere to regional regulatory requirements, thereby maximizing operational efficiency and cost-effectiveness.
Product Flexibility:
Encompass processes and machinery that can handle numerous product variations. This, in turn, can enable the plant to cater to diverse market demands.
Sustainability Features:
Incorporate various eco-friendly options, including renewable energy integration, waste management systems, energy-efficient machinery, etc., to meet sustainability goals.
Raw Material Sourcing:
Tailor the supply chain strategy to enable cost-effective and reliable access to raw materials specific to client requirements or the region.
Browse Related Reports:
Electrically Conductive Adhesive Manufacturing Plant
About Us: IMARC Group is a global management consulting firm that helps the world’s most ambitious changemakers to create a lasting impact. The company excel in understanding its client’s business priorities and delivering tailored solutions that drive meaningful outcomes. We provide a comprehensive suite of market entry and expansion services. Our offerings include thorough market assessment, feasibility studies, company incorporation assistance, factory setup support, regulatory approvals and licensing navigation, branding, marketing and sales strategies, competitive landscape, and benchmarking analyses, pricing and cost research, and procurement research.
Contact Us:
IMARC Group
134 N 4th St. Brooklyn, NY 11249, USA
Email: sales@imarcgroup.com
Tel No:(D) +91 120 433 0800
United States: +1-631-791-1145