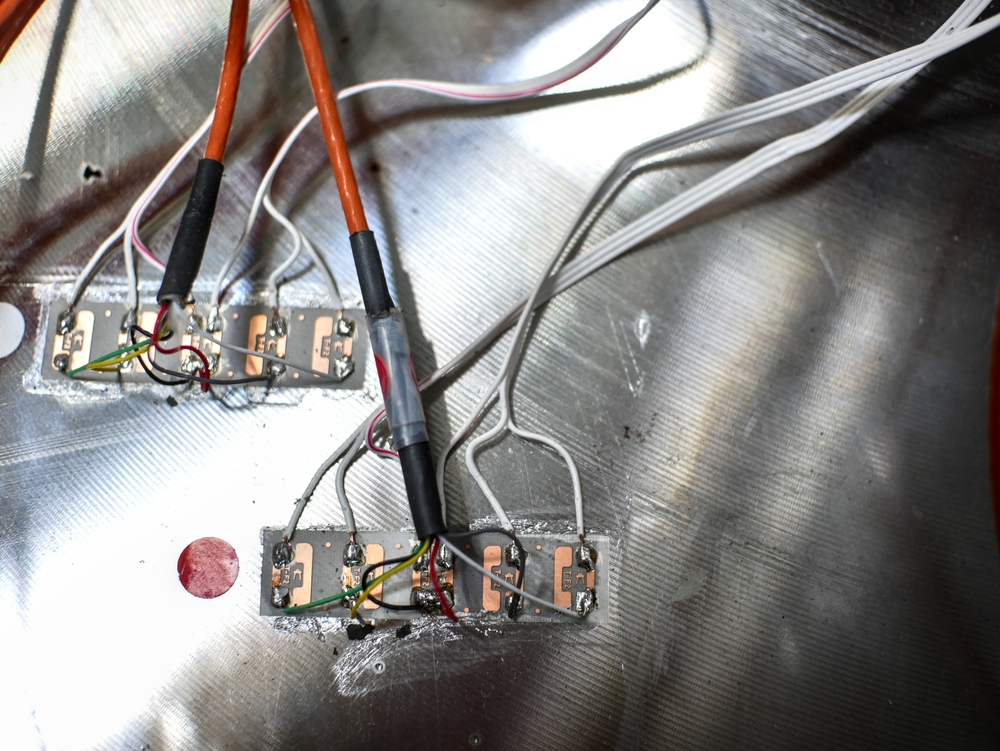
Strain Gauge: Understanding the Basics and Selecting the Right One
- Jul 12, 2023
- | 91
Strain gauges are essential components in a wide range of applications, from engineering to medical devices. But what exactly is a strain gauge, and how do you choose the right one for your specific needs? In this comprehensive guide, we?ll explore the world of strain gauges, delve into the different types available, and provide expert advice on selecting the perfect strain gauge for your application. So whether you?re a seasoned engineer or a newcomer to the field, read on to learn everything you need to know about strain gauges.
What is a Strain Gauge?
A strain gauge is a device used to measure the deformation or displacement of a material when subjected to an external force. This can be crucial in a variety of applications, such as stress analysis in engineering, monitoring structural integrity, and even measuring human muscle movement in medical devices. At its core, a strain gauge works by converting the mechanical strain experienced by a material into an electrical signal, which can then be measured and analyzed.
Types of Strain Gauges
There are several types of strain gauges available, each with its own unique characteristics and advantages. Some of the most common types include:
Mechanical Strain Gauges
These gauges utilize a mechanical system, such as a lever or spring, to measure strain. While they can be relatively simple and inexpensive, they may not offer the same level of accuracy and sensitivity as other types.Electrical Resistance Strain Gauges
These gauges measure strain by monitoring changes in electrical resistance. As the material deforms, the resistance of the strain gauge changes, allowing for precise measurements. This is the most common type of strain gauge used in industry today.Optical Strain Gauges
These gauges rely on changes in light transmission to measure strain. By monitoring the shift in light patterns, optical strain gauges can provide highly accurate and sensitive measurements.Semiconductor Strain Gauges
These gauges utilize the piezoresistive effect in semiconductor materials to measure strain. They offer high sensitivity and can be used in a variety of applications.Key Factors in Strain Gauge Selection
When selecting a strain gauge, there are several factors to consider, including:
Sensitivity
The sensitivity of a strain gauge refers to its ability to detect small changes in strain. Higher sensitivity is generally desirable, but it may come at the cost of increased complexity or expense.Accuracy
The accuracy of a strain gauge is its ability to provide precise measurements. This can be crucial in applications where small errors can have significant consequences.Temperature Range
Different strain gauges may have varying temperature ranges, which can impact their performance and suitability for certain applications.Material Compatibility
The strain gauge must be compatible with the material it is measuring, as some materials can cause interference or damage to the gauge.Environmental Factors
Consider the environment in which the strain gauge will be used, such as potential exposure to moisture, chemicals, or extreme temperatures.Strain Gauge Applications
Strain gauges can be used in a wide range of applications, including:
- Engineering: In engineering, strain gauges are often used for stress analysis, structural integrity monitoring, and material testing.
- Aerospace: Strain gauges can be used to monitor the structural integrity of aircraft components and to measure the stress experienced during flight.
- Automotive: In the automotive industry, strain gauges can be used to measure the stress experienced by components during operation, as well as for crash testing and safety analysis.
- Medical Devices: Strain gauges can be used to measure human muscle movement, providing valuable data for medical professionals and researchers.
- Civil Infrastructure: Strain gauges can be used to monitor the structural integrity of bridges, buildings, and other critical infrastructure.

Strain Gauge Installation Tips
Proper installation is crucial for obtaining accurate and reliable measurements from your strain gauge. Some key tips for strain gauge installation include:
- Surface Preparation: Ensure the surface where the strain gauge will be installed is clean, dry, and free of any contaminants.
- Adhesive Selection: Choose an appropriate adhesive for your specific application, considering factors such as temperature range and material compatibility.
- Gauge Alignment: Align the strain gauge with the direction of the expected strain to ensure accurate measurements.
- Wiring: Ensure proper wiring connections and avoid any potential sources of interference.
Strain Gauge Sensitivity and Accuracy
As mentioned earlier, sensitivity and accuracy are crucial factors in strain gauge selection. Sensitivity refers to the gauge's ability to detect small changes in strain, while accuracy pertains to the precision of the measurements. To ensure optimal performance, it is important to select a strain gauge with the appropriate sensitivity and accuracy for your specific application.
In general, electrical resistance strain gauges offer a good balance of sensitivity and accuracy, making them a popular choice for many applications. However, other types of strain gauges, such as optical or semiconductor gauges, may offer even higher levels of sensitivity and accuracy, depending on the specific requirements of your application.
Conclusion: Making the Right Choice
Selecting the right strain gauge for your application can be a complex process, but with a solid understanding of the basics and careful consideration of the factors discussed in this guide, you can make an informed decision that will ensure accurate and reliable measurements. By considering factors such as strain gauge type, sensitivity, accuracy, temperature range, material compatibility, and environmental factors, you can choose the perfect strain gauge for your specific needs and enjoy the benefits of precise strain measurement in your application.