Overcoming Installation Issues in Prefabricated Buildings
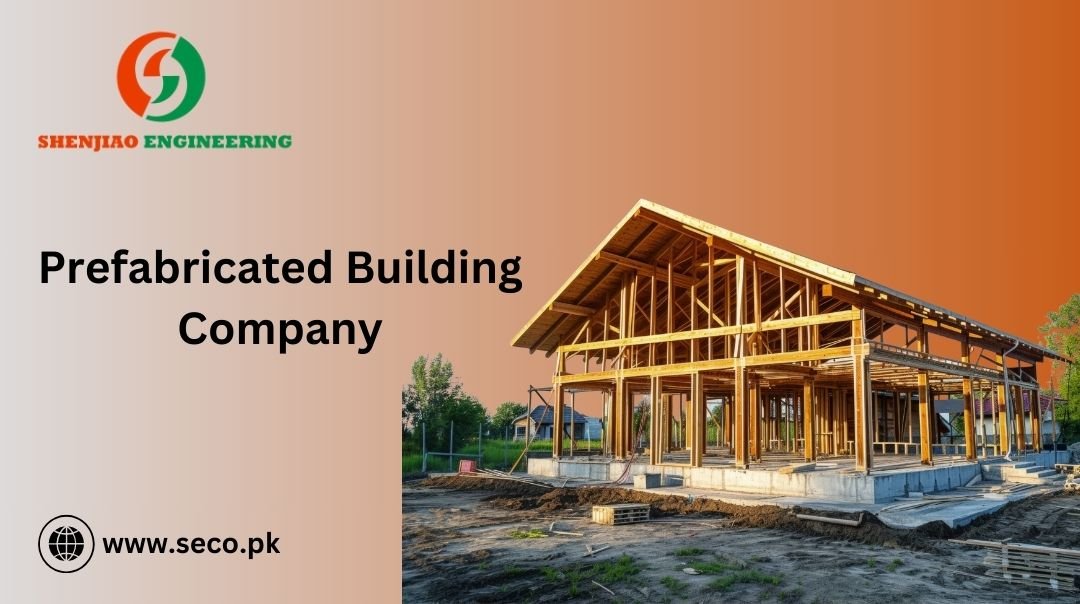
Prefabricated buildings have revolutionized the construction industry with their speed, efficiency, and sustainability. However, like any complex process, prefabricated building installation can encounter issues that hinder the smooth delivery of projects. In this article, we will discuss common installation challenges in prefabricated buildings and provide solutions to overcome them, ensuring a seamless and successful project outcome.
Design Incompatibilities
Prefabricated building design requires precise planning and coordination. Incompatibilities between modules or with on-site connections can lead to installation delays and cost overruns. To overcome this, prefabricated building construction company must ensure:
- Accurate site measurements and surveys
- Detailed design coordination with architects and engineers
- Utilization of Building Information Modelling (BIM) technology for precise modeling and clash detection
Logistical Challenges
Transporting and storing prefabricated modules require careful planning. Logistical issues can result in damaged modules, delayed delivery, and increased costs. To mitigate this:
- Collaborate with experienced logistics providers
- Ensure proper module packaging and protection
- Schedule timely delivery and installation
Site Preparation Issues
Prefabricated buildings require a prepared site with adequate foundation and utilities. Site preparation issues can delay installation and compromise the structure's integrity. To overcome this:
- Conduct thorough site assessments and geotechnical studies
- Ensure proper foundation design and installation
- Coordinate with utility providers for timely connections
Connection and Assembly Challenges
Prefabricated modules require precise connection and assembly. Issues with connections can compromise the structure's integrity and lead to costly rework. To overcome this:
- Utilize experienced installation teams
- Ensure accurate module alignment and connection
- Implement quality control measures during assembly
Weather and Environmental Factors
Prefabricated building installation can be affected by extreme weather conditions and environmental factors. To overcome this:
- Schedule installation during favorable weather conditions
- Utilize weather-resistant materials and protective coatings
- Implement environmental sustainability measures
In conclusion, prefabricated building installation requires meticulous planning, precise execution, and collaboration among stakeholders. By understanding and addressing potential installation issues, prefabricated building construction companies can ensure successful project outcomes, meeting the demands of modern construction projects.
By choosing a reputable prefabricated building construction company that prioritizes design coordination, logistical planning, site preparation, precise assembly, and environmental sustainability, clients can enjoy the benefits of prefabricated buildings while minimizing installation challenges.
Key Takeaways:
- Prefabricated building design requires precise planning and coordination.
- Logistical challenges can be mitigated with careful planning and collaboration.
- Site preparation is crucial for a successful installation.
- Connection and assembly require precision and quality control.
- Weather and environmental factors must be considered during installation.
By overcoming installation issues in prefabricated buildings, we can unlock the full potential of this innovative construction method, delivering efficient, sustainable, and high-quality buildings for generations to come.