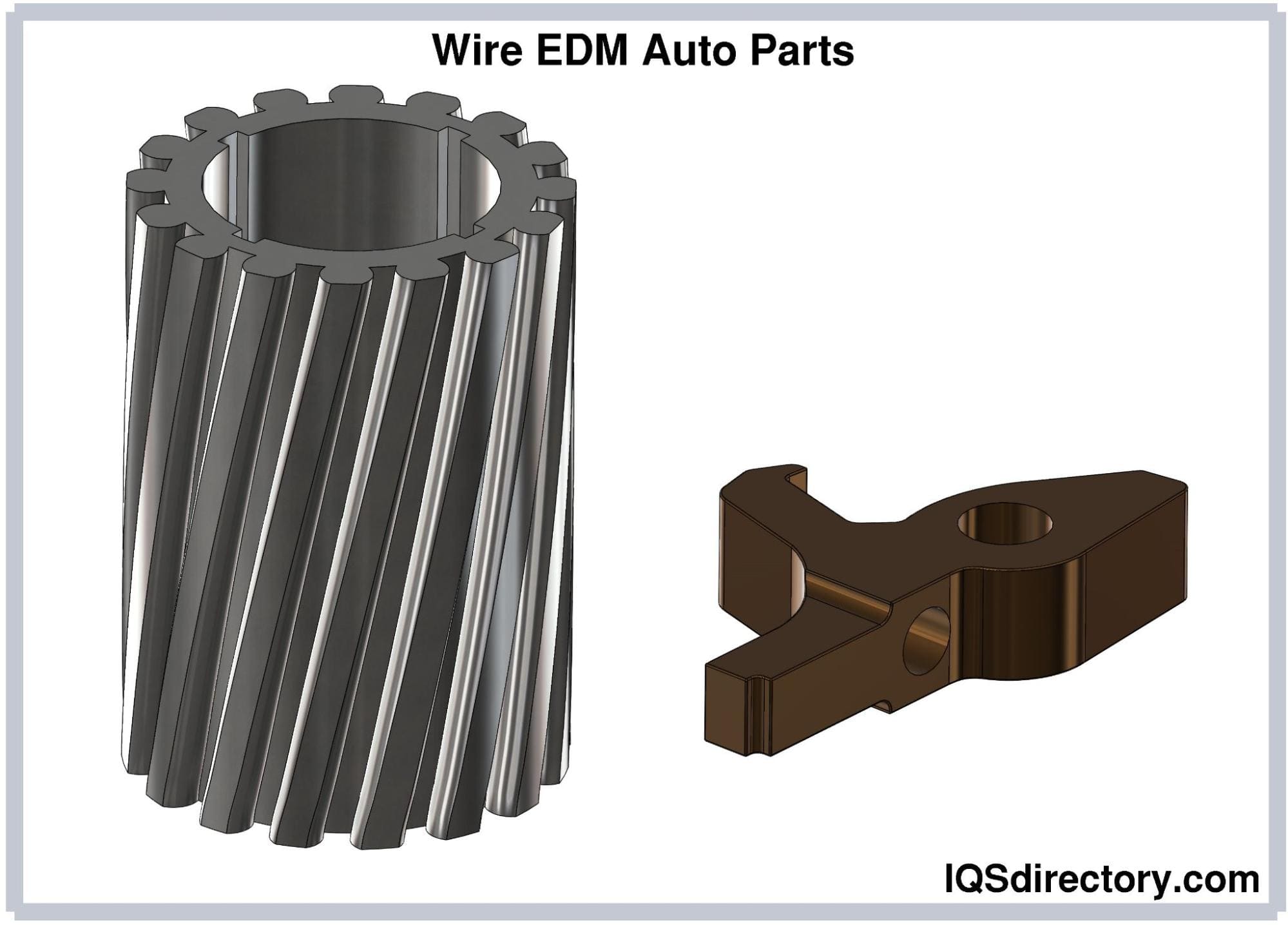
Optimizing Precision: A Comprehensive Guide to Wire EDM Parts and Fixtures
- Feb 23, 2024
- | 127
Wire Electrical Discharge Machining (EDM) is a cutting-edge process that has revolutionized precision machining in various industries. At the heart of this advanced technology lie crucial components, namely wire EDM parts and fixtures, which play a pivotal role in achieving optimal precision and efficiency in the machining process.
Understanding Wire EDM Parts:
Wire EDM parts are integral elements in the EDM process, contributing significantly to the accuracy and quality of machined components. These parts typically include wire guides, EDM blocks, and Guide Wheels, each serving a unique purpose in ensuring a smooth and precise machining operation.
Wire Guides:
Wire guides are essential components that guide the electrically charged wire through the material being machined. These guides come in various shapes and sizes, each designed for specific applications. High-quality wire guides ensure consistent and reliable performance, minimizing the risk of wire breakage and ensuring precise cuts.
EDM Blocks:
wire edm parts blocks, often made of materials like ceramics or carbide, provide structural support to the workpiece during the machining process. These blocks are meticulously designed to withstand the intense electrical discharges while maintaining stability, crucial for achieving intricate and precise cuts.
Guide Wheels:
Guide Wheels play a critical role in the wire EDM process by guiding the wire through complex cuts. Choosing the right Guide Wheel is paramount, as it directly impacts the accuracy and efficiency of the machining operation. Factors such as material composition, size, and design must be carefully considered to optimize precision.
Wire EDM Fixtures:
Wire EDM fixtures are another vital aspect of the machining process, working in tandem with wire EDM parts to secure and stabilize the workpiece. These fixtures are designed to hold the material firmly in place, preventing movement during the EDM operation. A well-designed fixture ensures consistent results and reduces the likelihood of errors.
Types of Fixtures:
There are various types of fixtures used in wire EDM, including clamps, vises, and specialized custom fixtures. The choice of fixture depends on the specific requirements of the job, such as the size and shape of the workpiece, the desired cut, and the material being machined.
Advantages of Quality Fixtures:
Investing in high-quality fixtures pays off in terms of increased efficiency and precision. Quality fixtures provide stability, reduce vibration, and allow for repeatable setups, ultimately leading to a higher quality finished product.
Best Practices for Optimizing Precision:
- Material Selection: Choose wire EDM parts and fixtures made from high-quality materials that can withstand the demands of the machining process.
- Regular Maintenance: Conduct routine maintenance on wire guides, EDM blocks, and fixtures to ensure longevity and consistent performance.
- Customization for Specific Applications: Tailor your choice of wire guides, EDM blocks, and fixtures based on the unique requirements of each machining job.
- Calibration and Alignment: Regularly calibrate and align wire EDM parts and fixtures to maintain accuracy and prevent deviations in machining.
- Training and Skill Development: Provide adequate training for operators to ensure they understand the intricacies of using different wire EDM parts and fixtures effectively.
Conclusion:
In conclusion, optimizing precision in wire EDM involves a meticulous understanding and utilization of wire EDM parts and fixtures. By selecting high-quality components, implementing best practices, and investing in proper training, manufacturers can unlock the full potential of wire EDM technology, achieving unparalleled precision and efficiency in their machining operations.