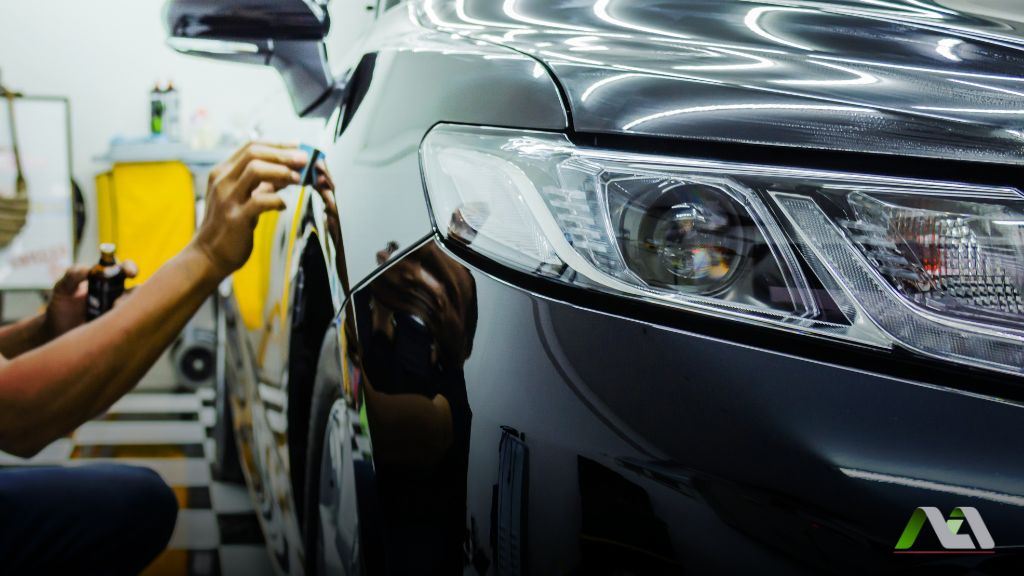
Among the various types of metals being used in industries today, lightweight metals are seen to be ideal in every aspect. Traditional metals are aluminum, titanium, etc., and more recently, a new-age metal like magnesium has gained importance in automotive as well as aerospace applications. Their availability, high strength-to-weight ratios, and suitability for most applications make them a material of first choice. Nonetheless, selecting the correct metal protection can seriously improve the quality, outlook, and efficiency of your work. Given the many varieties in the market, it becomes difficult to identify which specific coat type is most appropriate for your application.
Types of Metal Protection Coatings
- Powder Coating
This method of coating metal has become widely used due to its durability, non-toxicity to the environment, and availability of various colors and types of the final product. This sort of finishing technique involves the application of powder paint on the surface of the metal that is subsequently heated and polymerized to form a coat. The powder coating has the advantage of giving a smooth, attractive, and long-lasting surface, which is also less prone to chipping, scratching, or fading.
- Galvanizing
Galvanizing is a process whereby metal is coated with zinc to keep it from rusting. It is usually done through hot-dip galvanizing, in which the metal is Immersed in a tank of molten zinc, or through the electro-galvanizing process that uses an electrical current to deposit the zinc layer. These coatings are especially beneficial In preventing the formation of rust and increasing the service life of metal elements exposed to aggressive environments.
- Electroplating
Electroplating involves coating a metal or any other part with one or more metals, including chrome, nickel, gold, etc. This method can act both as a decorative finish but also improve the corrosion and wear properties of the metal in question. Electroplating is widely used in automotive, aerospace, and consumer electronics industries, where parts made of metals must be coated to enhance their functionality, appearance, and durability.
Benefits of Metal Protection Coatings
- Complete Protection
Protective coatings for metal cover up layers of metallic elements or metal alloys, which can be deposited on the metal surface. These applications also help offer multiple layers of protection from oxidation, corrosion, and the effects of sunlight, and they give a glossy appearance. Anti-rust coatings change the surface chemistry and protect it from environmental influences, which is why they are used in many sectors.
- Durability
Developing an intermediate barrier insulates the surface from wear and tear and greatly increases the life and toughness of the product. Anti-corrosive coatings enhance the lifespan of metal structures while minimizing the frequency of maintenance.
- Aesthetics
Aesthetics may be important in certain cases depending on the type of work being done and the sector involved. Choosing a metal coating that maintains or even enhances the appearance can be a great option, ensuring that the project looks good while being protected. The use of high-quality finishes is a plus to the final output of the construction and serves to give the product a more aesthetic look.
- Greater Performance
Applying protective coatings on metal increases the performance of the material used in the fabrication of electronic equipment by improving the electrical characteristics and conductivity of the material. These coatings sometimes offer other advantages, including increased wear resistance and enhanced heat dissipation. In production processes like marine and manufacturing, anti-corrosive coatings play a significant role in conserving metal products from corrosion, among other hazards.
Applications of Metal Protection
Automotive Industry
In automotive industries, metal protection is very essential, especially on parts that are exposed to extreme weather conditions. To decrease the amount of rust and corrosion, processes such as galvanizing and electroplating are applied. It enhances the lifespan and quality of car parts. Powder coating is preferred for its appearance as well as its corrosion and abrasion resistance. Therefore, this technology is suitable for both exterior and interior components.
Aerospace Industry
Aerospace sectors require reliable and long-lasting coatings that can function optimally under harsh environmental conditions. For metals such as aluminum and titanium, which are relatively light, the added layer of protection from coatings is highly valuable due to their increased susceptibility to corrosion and wear. These coatings ensure that aerospace components maintain their integrity and performance over long periods.
Consumer Applications
In consumer electronics and appliances, metal protection coatings are used to improve appearance, durability, and functionality. Electroplating is commonly used to provide a sleek, decorative finish while offering added protection against wear and tear. Powder coating provides a versatile and durable option for various consumer products, ensuring long-lasting and attractive finishes.
Conclusion
Investing in high-quality metal protection is essential for enhancing the durability, appearance, and performance of your project. The right coating can make a significant difference in maintaining the integrity and functionality of metal components across various industries. As technology advances, the capabilities of these coatings will continue to improve.