Corrosion Resistance Testing: How Salt Spray Chambers Ensure Material Longevity
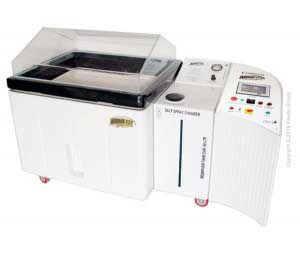
In various industries, ensuring the durability and long-term performance of materials is crucial. One of the most effective ways to assess how materials withstand harsh environmental conditions, especially corrosion, is through the use of a salt spray chamber. This advanced testing equipment simulates the corrosive effects of saltwater environments, providing manufacturers with valuable data on the durability of their products. In this blog, we’ll delve into the functionality, importance, and applications of salt spray testers and salt spray test chambers.
What is a Salt Spray Chamber?
A salt spray chamber (also known as a salt spray tester or salt spray test chamber) is a specialized testing device designed to evaluate the resistance of materials, coatings, and products to corrosive environments, particularly salt-laden air. The test involves exposing the specimen to a controlled mist of saltwater, simulating the harsh conditions materials may face when exposed to saltwater environments, such as in marine or coastal applications.
How Does a Salt Spray Test Work?
A salt spray test is relatively simple but effective. The specimen, usually made from metal, plastic, or coated materials, is placed inside the chamber, where it is subjected to a fine mist of saltwater (typically sodium chloride solution) at a constant temperature and humidity level. The test chamber is equipped with specific controls that allow the operator to adjust factors such as temperature, humidity, and the concentration of the salt solution. The chamber also maintains consistent airflow to simulate the effect of wind and other environmental factors.
The primary goal of the salt spray test is to accelerate the natural corrosion process, helping engineers determine how long a material will last when exposed to the corrosive effects of saltwater. The results can help manufacturers identify the best materials, coatings, and finishes for products that will be exposed to such environments.
Types of Salt Spray Chambers
There are different types of salt spray test chambers, each designed to cater to specific testing requirements. Some of the most common types include:
-
Continuous Salt Spray Chamber – This is the most commonly used type, where the salt solution is continuously sprayed over the specimen for an extended period.
-
Intermittent Salt Spray Chamber – In this chamber, the salt mist is applied in intervals. This method is particularly useful for simulating natural conditions, such as intermittent exposure to salty environments.
-
Cyclic Corrosion Test Chamber – This advanced chamber mimics the natural cycles of corrosion that occur in real-world conditions, combining salt spray with changes in temperature and humidity to simulate environmental shifts.
Importance of Salt Spray Testing
-
Corrosion Resistance Evaluation: The primary function of a salt spray chamber is to evaluate the corrosion resistance of materials. Corrosion can lead to product failure, safety hazards, and high maintenance costs, especially in industries such as automotive, marine, and construction. Salt spray testing helps manufacturers assess whether their materials and coatings are capable of withstanding these conditions over time.
-
Material and Coating Selection: Salt spray testing assists in choosing the best material or protective coating for specific applications. Whether it's choosing a corrosion-resistant alloy or testing a new coating for durability, the results from a salt spray test can guide manufacturers in making more informed decisions.
-
Quality Control: For manufacturers, maintaining consistent quality is vital. The salt spray test chamber provides a standardized method for evaluating the durability of their products and ensuring that they meet industry standards. This can help prevent costly product recalls and maintain brand reputation.
-
Industry Standards Compliance: Various industries, such as automotive and aerospace, have strict standards for material and product durability. Salt spray testing helps companies meet the necessary specifications, ensuring their products pass the required certifications.
Applications of Salt Spray Testing
Salt spray testing is widely used in industries that deal with materials exposed to harsh environments. Some of the primary applications include:
-
Automotive Industry: Components such as car bodies, wheels, and engine parts are regularly tested for corrosion resistance to ensure they can withstand exposure to salty road conditions, especially in coastal areas or during winter months when roads are salted.
-
Marine Industry: Boats, ships, and offshore structures are tested for corrosion due to saltwater exposure. Salt spray testing ensures these structures are robust and long-lasting, providing safety and reliability.
-
Aerospace Industry: Aircraft components are exposed to a variety of harsh conditions, including saltwater in coastal areas or salt used in de-icing. Salt spray testing helps ensure the longevity and safety of these components.
-
Construction: Steel and other materials used in construction projects are tested to assess their ability to resist corrosion in coastal or high-humidity environments.
Benefits of Salt Spray Testing
-
Accelerated Testing: Salt spray testing accelerates the natural corrosion process, allowing manufacturers to evaluate materials in a fraction of the time it would take under real-world conditions.
-
Reliable Results: The controlled environment of the salt spray chamber ensures consistent, repeatable test results, making it an essential tool for quality control and product development.
-
Cost-Effective: By testing materials in a salt spray chamber before production, manufacturers can identify potential failures and weaknesses, reducing the risk of costly product failures and recalls.
Conclusion
In conclusion, salt spray testers and salt spray test chambers are essential tools in evaluating the corrosion resistance of materials, coatings, and finished products. With the ability to simulate the harsh effects of saltwater exposure, these testing instruments play a critical role in ensuring the longevity and durability of products in industries such as automotive, marine, aerospace, and construction. Whether for quality control, material selection, or meeting industry standards, salt spray testing provides invaluable insights into product performance in real-world, corrosive environments.