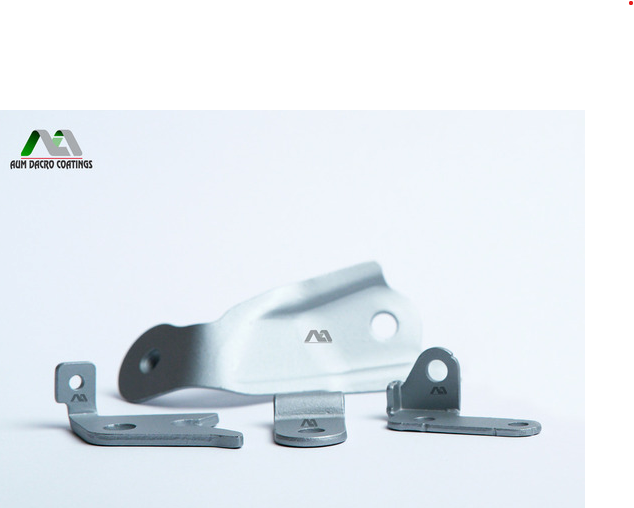
Corrosion Protection: Protect Your Industrial Setting
- Nov 06, 2024
- | 33
Corrosion is a major problem in the industrial world. This can cause necessary damage to the structures and other equipment that leads to costly repairs and downtimes. In this resource, you will learn about corrosion, the way it affects industries, and effective methods to protect your industrial components. You should also know about effective corrosion protection techniques to enhance the strength of durable components.
What is the Importance of Corrosion Protection?
Corrosion protection can help in several economic benefits. You can protect your infrastructure and other equipment by avoiding costly repair and replacement expenses. Proper maintenance and protection will help you improve operational efficiency and reduce maintenance costs in the long run.
Corrosion affects business and has a certain impact on environmental issues. Hence, by implementing corrosion protection, you can prevent environmental damage by reducing the risk of leaks and spills. The zinc coating market has reached up to USD 1.48 billion and will increase further.
When Should You Go for Corrosion Protection?
The transportation industry has a wide impact on corrosion due to exposure to harsh environmental conditions like humidity, saltwater, and varying temperatures. This process will lead to structural degradation and cause necessary safety issues. The movement of goods and vehicles can lead to more damage. Proper corrosion protection will ensure the longevity and safety of goods transported in such complex situations.
How Zinc Flake Coating Provides Super Protection?
Zinc flake coating is a type of non-electronic coating method where small zinc particles are applied to the metal surfaces. The traditional process involves diving materials within the molten zinc. At the same time, zinc flake coating thickness is applied through baking and chemical bonding. This process provides super protection without the risk of hydrogen embrittlement for durable material.
What is the Requirement of Zinc Flake Coating?
The thickness of the applied layers has a major impact on the effectiveness of zinc flake coating. The zinc flake coating thickness usually falls between 8 and 20 micrometres. The zinc flake layer's performance is directly impacted by its thickness; an excessively thick coating might result in decreased efficacy, while a too-thin coating can lead to dimensional issues. The optimal coating thickness depends on a number of parameters, including.
- Environment: Thicker coatings offer superior resilience and longer-lasting protection in extremely corrosive situations.
- Application Requirements: The required coating thickness will depend on the component's anticipated service life and operating conditions. For example, in order to achieve strict durability criteria, automotive nuts and fasteners could require thicker layers.
- Type of Metal Substrate: Various coating thicknesses may be needed for the best protection depending on the substrate type, such as steel or aluminium.
What are the Facilities for Zinc Flake Coating?
- Superior Corrosion Protection: Zinc flake coating thickness is very beneficial for components exposed to wet and saline conditions since they can withstand salt spray for up to 1,000 hours.
- Environmental Compliance: A lot of zinc flake coatings do not contain chromate, which complies with laws that restrict the use of heavy metals like hexavalent chromium.
- Temperature Resistance: Zinc flake coatings are durable in high-temperature applications because they can tolerate temperatures of up to 300°C (572°F).
- Resistance to Hydrogen Embrittlement: Zinc flake coating is appropriate for high-tensile-strength components because, in contrast to electroplating, it does not inject hydrogen into the substrate.
How Does Magni Coating Help in Structural Applications?
The Magni coating process is a perfect combination of organic zinc with another organic topcoat. Due to proper coating and resistance to automotive fuel, this process for coating has preferred proper coating for the automotive industry. This coating is seen in the automotive industry, which has adopted the capabilities of coating systems for structural and tower applications.
The Magni coating process offers fasteners exceptional corrosion protection in the field. Unlike hot dip galvanising, which usually uses an acid pickling process and needs fasteners to be submerged in molten zinc, Magni coatings eliminate the hydrogen embrittlement issues related to coating high-strength fasteners.
What are the Applications of Mangi Coatings and Zinc Flakes?
With their adaptable and potent protective qualities, magnesium and zinc flake coatings are used in a variety of sectors. Here are a few noteworthy uses to consider.
- Automotive Industry: Bolts, nuts, and other fasteners in automobiles are frequently coated with magnesium and zinc flake. These coatings shield metal parts from the damaging effects of chemicals, water, and salt that are present in road settings.
- Construction and Infrastructure: Zinc flake coatings and the Magni coating process reduce maintenance requirements and increase structural lifetime by offering long-lasting protection for metal structures and fittings exposed to outside conditions.
How Does Corrosion Protection Help to Maintain the Quality of the Material?
Corrosion protection is necessary to maintain the durability and strength of the metal parts. These coatings are effective methods to get exceptional protection. It is necessary to understand the importance of coating thickness. Consider the right industries, like Aum Dacro Coatings, to ensure lasting durability.