10 Best Practices for Safe Operation of a Wood Pellet Production Line
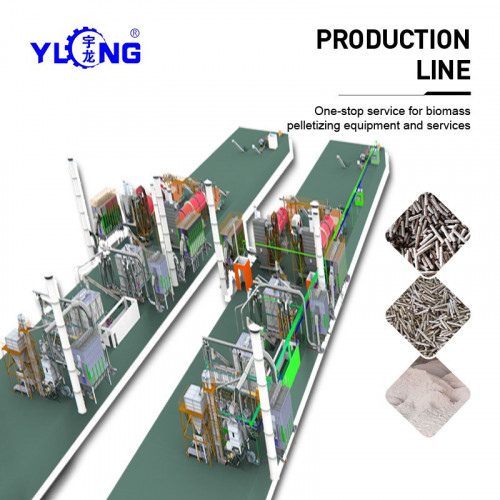
Wood pellets, known for their sustainability and high energy content, have become an increasingly popular renewable energy source. As the global demand for these eco-friendly pellets rises, so does the urgency for maintaining safety standards in their production.
This blog delves into the essential practices for running a wood pellet production line safely, ensuring the well-being of operators and the efficiency of the production process.
1. Understanding the Risks
Before diving into the best practices, it's crucial to understand the risks inherent in wood pellet production. The primary dangers include fire hazards due to the combustibility of wood dust and pellets, health risks from dust inhalation, and physical safety concerns around machinery. Identifying these risks is the first step in mitigating potential accidents and hazards.
2. Comprehensive Training
Safety starts with knowledge. Providing comprehensive training to all employees involved in the production line is paramount. This training should cover the operation of machinery, emergency response procedures, and the correct use of personal protective equipment (PPE). Special attention should be given to fire safety training, given the highly flammable nature of the raw materials and final products.
3. Utilizing Personal Protective Equipment
Personal Protective Equipment (PPE) is a critical aspect of maintaining safety. Operators should wear protective gear, including dust masks or respirators to prevent inhalation of harmful wood dust, safety goggles for eye protection, and gloves to protect hands from sharp objects and machinery. Ensuring that all personnel are equipped with the appropriate PPE according to their job specification greatly reduces the risk of injuries.
4. Dust Management and Ventilation
Wood dust not only poses a health risk but is also a major fire hazard. Implementing a rigorous dust management system to collect and remove dust from the production area is vital. This includes installing dust extraction and ventilation systems that are regularly inspected and maintained. It's equally important to ensure that these systems are correctly sized for the production capacity to handle the volume of dust produced efficiently.
5. Regular Maintenance and Inspection of Machinery
The machinery used in wood pellet production requires regular maintenance and inspection to ensure it operates safely and efficiently. This includes checking for wear and tear, ensuring that safety guards are in place and functioning, and verifying that emergency shut-offs are accessible and fully operational. A routine maintenance schedule can prevent many accidents and machinery malfunctions.
6. Strict Adherence to Operating Procedures
Standard Operating Procedures (SOPs) are developed for a reason—to ensure every process is completed safely and correctly. Adherence to these procedures should be non-negotiable, with clear guidelines in place for every aspect of the production line. This includes instructions for starting and stopping machinery, clearing blockages, and responding to emergencies. SOPs should be easily accessible to all employees and regularly reviewed and updated as needed.
7. Fire Prevention and Emergency Preparedness
Given the combustible nature of wood pellets and dust, fire safety cannot be overstressed. Facilities should be equipped with automatic sprinkler systems, fire extinguishers, and fire alarms strategically located throughout the production area. Conducting regular fire drills will ensure that employees know how to respond in the event of an emergency, which can dramatically reduce the risk of injury and property damage.
8. Safe Storage Practices
The way wood pellets are stored can also present hazards. Pellets should be stored in a dry, well-ventilated area to reduce the risk of degradation and spontaneous combustion. It's crucial to avoid overloading storage areas, which can create unstable conditions prone to accidents.
9. Continuous Safety Audits
Regular safety audits are essential to identify potential hazards that could lead to accidents or decreased production efficiency. These audits, conducted by safety professionals, should assess all aspects of the production line, from raw material intake to the final pellet storage. The findings should then be used to make necessary adjustments and improve safety measures continuously.
10. Encouraging a Safety-First Culture
Finally, creating a culture that prioritizes safety above all else is one of the most effective ways to ensure a safe working environment. This involves not only training and procedures but also encouraging employees to speak up about potential hazards and providing channels for doing so without fear of retribution. A safety-first culture is built on mutual respect, open communication, and a shared commitment to the well-being of all employees.
In conclusion, the safe operation of a wood pellet production line requires a multi-faceted approach that includes thorough training, strict adherence to safety procedures, regular maintenance, and a company culture that values safety. By implementing these best practices, and also consulting your large pellet mill supplier, producers can mitigate risks, protect their workforce, and ensure the smooth and efficient production of wood pellets. Remember, a safe production line is also a productive and profitable one.